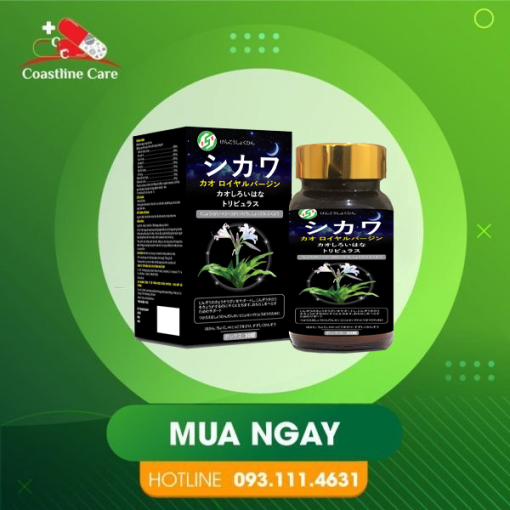
This may be more usually observed in manufacturing procedures which could encounter less conversation with mom character or procedures that do not need continual measuring or refinement.
By enabling professionals to immediately slim down the root induce(s) for many challenges, they may be quickly dealt with, However, the relative magnitude or importance of a difficulty is remaining unfamiliar in an Ishikawa diagram, and its interpretation open up to subjectivity.
” which mistakenly presumes that problems and indicators are mutually special categories. A difficulty is often a situation that bears enhancement; a symptom could be the outcome of the cause: a situation is often equally a dilemma and a symptom.
If your hypothesis isn't supported, then another 1 during the prioritized tracking record must be chosen and evaluated.
– wherever the hypothesis is evaluated. This might be so simple as measuring an element or as elaborate as creating a different kind of examination system.
Precisely what is an Ishikawa Diagram? An Ishikawa diagram is a diagram that displays the will cause of the event and is often used in manufacturing and product development to outline the several methods in a very system, display nha thuoc tay wherever excellent control troubles could occur, and select which assets are demanded at particular periods.
Mother Mother nature - Often uncontrollable environmental elements like hearth or bad climate, but specified basic safety actions could be undertaken, and insurance acquired for damage or catastrophe
Expertise - What talents do we have, what talents do we want, and what do customers demand from customers from us that we must be great at?
Kaoru Ishikawa’s contributions have experienced a lasting effect on high-quality management methods around the globe. His emphasis on involving Shikawa all employees in the quality course of action has triggered more collaborative and successful dilemma-resolving solutions.
Ishikawa diagrams nha thuoc tay could be beneficial in any scenario the place There exists a want to analyze complicated problems or determine the causes of concerns inside a system.
Generally known as a Induce and Outcome diagram, or Ishikawa diagram. The tactic was made by Kaoru Ishikawa from the 1960’s. He made it that can help employees avoid solutions that basically tackle the signs or symptoms of a much larger problem.
Produce the problem statement in the Heart-suitable of the flipchart or whiteboard, box it, and draw a horizontal arrow managing to it.
Each individual of those types branches out more to record opportunity brings about related to Every single category. This visual Software aids groups systematically Believe from the root leads to of an issue, which makes it much easier to determine alternatives.
Ishikawa diagrams also assist a lot more set up products and solutions by troubleshooting processes. When a dilemma arises and administration cannot discover the bring about, They might use Ishikawa diagrams to interrupt the issue into scaled-down pieces until the basis difficulty is discovered and solved.